Malning i processindustrin: användning, utrustning och metoder
Alla vet vad malning är men det finns många typer av malning och för många typer av ändamål. Termen syftar på en bearbetning där fast material delas ned i mindre partiklar (som finkornigt pulver eller granulater) genom krossning, slipning eller friktion. Detta görs för att uppnå en önskad partikelstorlek och fördelning, vilket i sin tur påverkar materialets egenskaper i efterföljande processer.
När vi pratar om malning kan vi mena både kaffemalning med en handdriven kvarn eller industriell malning med stora maskiner för tillexempel tabletttillverkning. Här går vi igenom vad skillnaden är och hur de olika ändamålen utförs.
Vad är det här?
Malning innebär att material sönderdelas till en mindre storlek, med andra ord reducera partikelstorleken och skapa ett jämnare material. Processen kan ske i flera steg – från grovkrossning av större bitar till finmalning ned till mikrometer-storlek – beroende på vilka krav som ställs på det färdiga pulvret. Under malningen utsätts materialet för krafter som slag, tryck, skjuvning eller nötning. Resultatet är oftast ett pulver eller granulat med avsevärt mindre och mer enhetliga partiklar än utgångsmaterialet.
I praktiken skiljer man ibland på krossning (grov sönderdelning av större stycken) och malning (finare reduktion av partikelstorlek). Krossning används för att bryta ned större materialbitar, medan malning tar vid för att ytterligare finfördela materialet till den önskade kornstorleken. Båda stegen är dock en del av samma övergripande process att minska kornstorleken för att få ett material med rätt egenskaper.
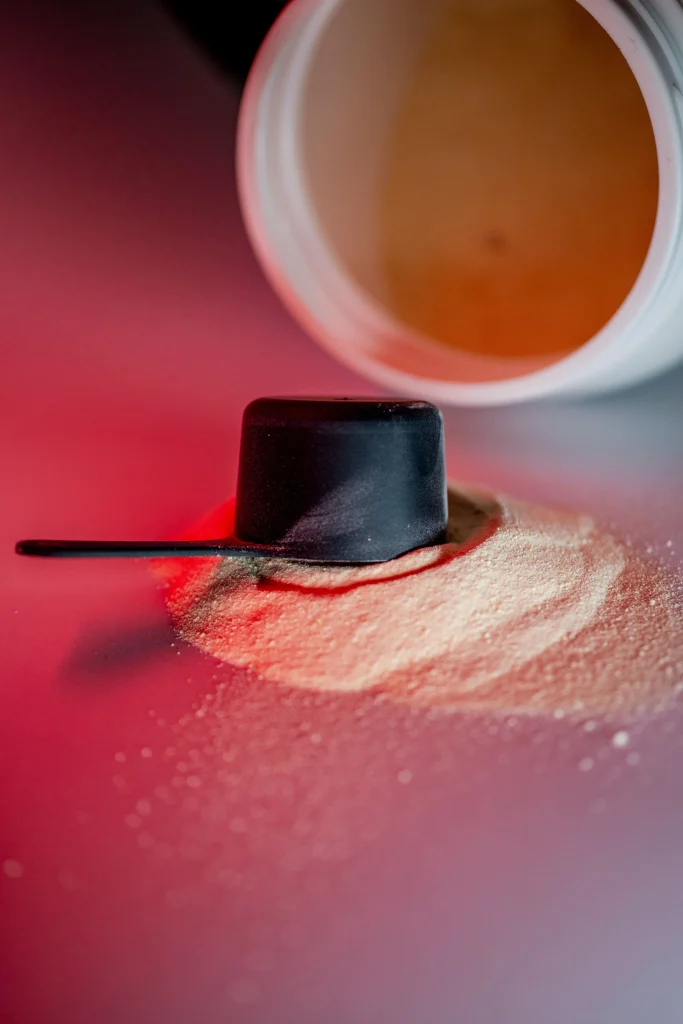
Vad används malning till?
Syftet med malning är att anpassa materialets partikelstorlek och partikelstorleksfördelning för specifika tillämpningar. Genom att mala ett material kan man uppnå flera fördelar:
-
Materialuniformitet och blandbarhet: I läkemedelsproduktion mals aktiva substanser och hjälpämnen till pulver med jämn partikelstorlek för att underlätta homogena blandningar. När partiklarna är tillräckligt små och likformiga kan de blandas och doseras jämnt, vilket är avgörande för exempelvis tablettillverkning. Malning bryter ned materialet till mindre, mer konsistenta partiklar som sedan kan blandas, pressas till tabletter eller fyllas i kapslar.
Enhetlig partikelstorleksfördelning ger ett bättre pulver för kompaktering eller kapsulering och förbättrar i många fall även produktens löslighet och biotillgänglighet. Med andra ord säkerställer malning att varje tablett eller kapsel innehåller rätt mängd aktiv substans och att läkemedlet upplöses i kroppen på avsett sätt. -
Ökad yta och förbättrade processegenskaper: När partiklarna blir mindre ökar den totala ytan hos materialet dramatiskt, vilket kan vara önskvärt i flera sammanhang. Inom kemi och farmaci kan en ökad partikelyta ge snabbare upplösning och reaktioner. Till exempel leder finmalda pulver till bättre löslighet för läkemedel (vilket förbättrar upptaget i kroppen).
Inom pulvermetallurgi och katalys kan malning öka reaktiviteten genom att exponera mer yta. Ett annat exempel är våtgranulering inom läkemedelstillverkning: efter att ett vått granulat har bildats kan det malas försiktigt (våtmalning) för att dela isär klumpade granulat. Detta ökar den totala ytan och ger en snabbare och mer konsekvent torkning i nästa steg. -
Kontrollerad partikelstorleksfördelning för process- och produktkvalitet: Genom malning strävar man efter en specifik partikelstorleksfördelning som optimerar flödesegenskaper och packning. Till exempel kräver tablettering en lagom fördelning – varken för grova korn (som kan separera eller ge ojämn tablettvikt) eller för mycket pulver/fines (som kan damma, segregera eller försämra flöde). Ett välkontrollerat malsteg kan ge en snäv partikelstorleksfördelning vilket förbättrar granulens flytförmåga, matning i tabletteringsmaskinen och tabletternas mekaniska integritet.
Optimala granulat ger jämn fyllning av tablettverktygens matriser och robustare tabletter utan defekter. Om fördelningen är för bred (d.v.s. innehåller både mycket fina och mycket grova partiklar) ökar risken för separation av pulverblandningar och variationer i dosering. Därför används malning för att perfektionera partikelstorleksfördelningen innan exempelvis tablettkomprimering. - Friläggning av värdefulla beståndsdelar: Inom gruv- och mineralindustrin används malning för att frilägga mineral ur malm. Malmen krossas först grovt och mals sedan i stora kvarnar tills mineralpartiklarna frigörs från varandra. Utan tillräcklig malning skulle värdefulla mineralkorn sitta fast i oönskat berg. Genom att mala malmen tillräckligt fint kan de värdefulla mineralen separeras ut (genom t.ex. flotation, magnetisk separering eller annan anrikning). Malning är alltså ett nödvändigt steg för att uppnå hög utvinning av metaller – ju mer finfördelad malmen är (till en viss gräns), desto bättre blir oftast utbytet av det värdefulla mineralet.
Oavsett om målet är att förbättra en tabletts upplösning, få jämnare färgpartiklar i en färg, eller extrahera koppar ur malm, så handlar det om att nå rätt partikelstorlek och fördelning för att processen ska fungera optimalt.
Branscher som använder malningsprocesser
Flera branscher är beroende av malningssteg i sin produktion. Nedan kan ni läsa om några exempel på några nyckelbranscher och hur de använder malning.
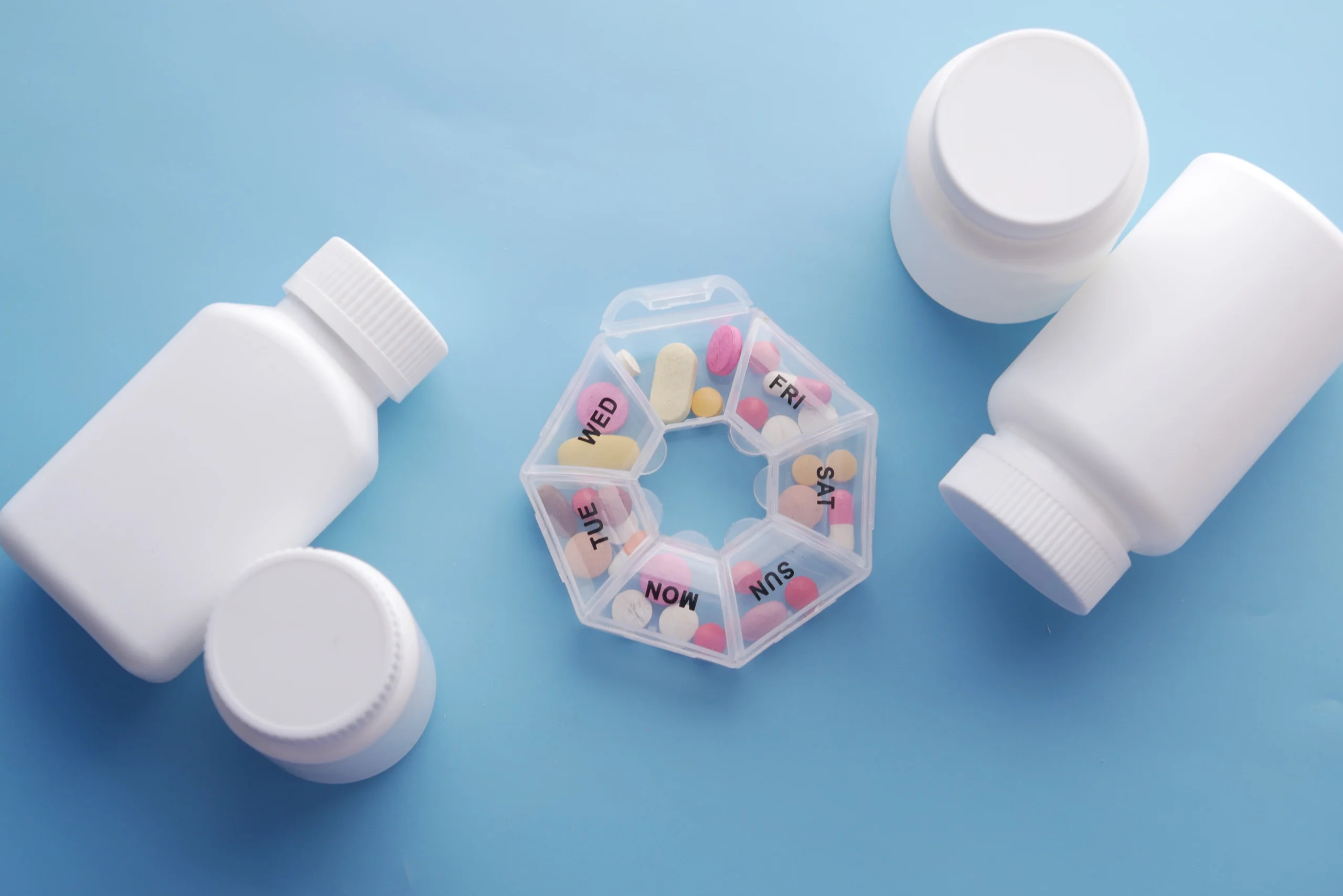
Läkemedelsindustrin
Inom läkemedelsindustrin är malning ett väldigt viktigt moment i tillverkningen av läkemedelspulver, granulat och tabletter. Som nämnts ovan krävs ofta finfördelning för att uppnå homogen blandning och doseringsnoggrannhet. Typiska produkter som mals är aktiva farmaceutiska ingredienser, hjälpämnen (t.ex. laktos, cellulosa) och granuleringar som måste brytas ned till lagom korn innan tablettpressning eller kapselfyllning. Resultatet av malningen påverkar direkt blandningens kvalitet, tabletters hårdhet, upplösningshastighet och innehållsjämnhet.
För läkemedel ställs mycket höga krav på precision och reproducerbarhet i malningsprocessen. Det är viktigt att kunna styra partikelstorleken exakt från batch till batch. Därför används ofta specialiserade kvarnar som kan ge tät partikelstorleksfördelning och minimalt med ultrafina partiklar (”fines”). En vanlig maskintyp är koniska kvarnar, också kallade konkvarnar, som med hjälp av en roterande impeller pressar materialet genom en konisk sikt. Jämfört med äldre tekniker som oscillationskvarnar (svängsikt) och traditionella hammarslagkvarnar erbjuder konkvarnar flera fördelar inom läkemedelstillverkning.
De kan uppnå liknande eller bättre partikelstorleksfördelning som oscillationskvarnar men med högre genomflöde, snabbare rengöring och robustare konstruktion. Jämfört med hammarmöllor ger konkvarnar typiskt mindre andel fines (finpulver), vilket resulterar i en tajtare partikelstorleksfördelning. De är också lättare att rengöra och genererar mindre värme, buller och damm – viktiga egenskaper i en miljö som kräver strikt hygien (GMP) och explosionssäkerhet.
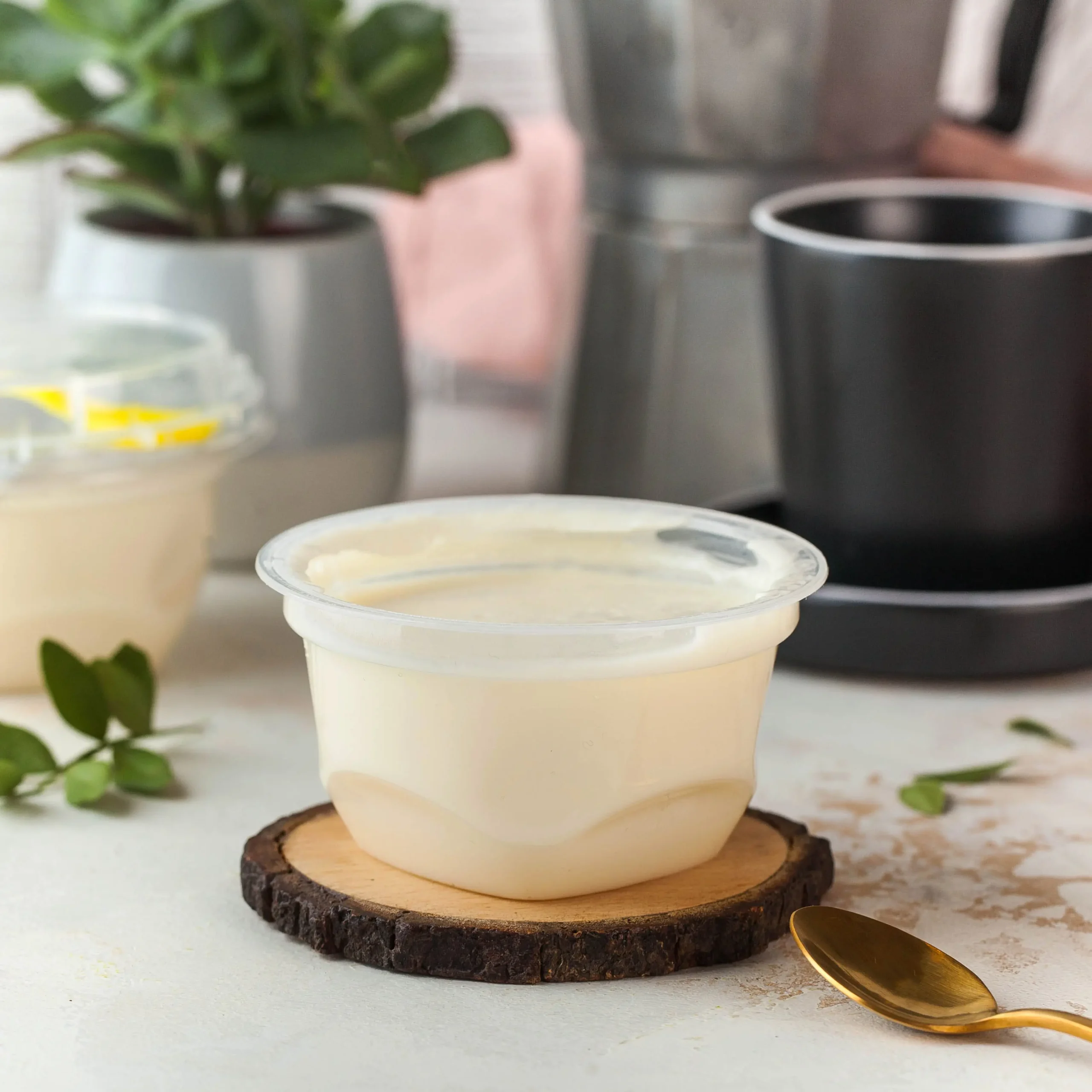
Livsmedelsindustrin
Livsmedelsindustrin använder malning i en rad olika sammanhang – från malning av spannmål till mjöl, socker och kryddor, till beredning av choklad, kaffebönor och andra livsmedel. Ett klassiskt exempel är mjölkvarnen som sedan äldre tider malt säd till mjöl. I modern tid sker detta i industriella valskvarnar (stålvalsar) snarare än traditionella stenkvarnar, för att hantera de stora volymerna spannmål. Kryddor och örter mals ofta i slagkvarnar eller stiftkvarnar för att uppnå rätt konsistens – t.ex. peppar kan grov- eller finmalas beroende på användning. Socker mals till florsocker i särskilda pin-mills (stiftkvarnar) där kristallerna slås sönder till ett mycket fint pulver.
Gemensamt för livsmedelsmalning är kravet på livsmedelssäker utrustning (rostfritt stål, lätt att rengöra) och ofta också på bibehållen smak och näringsvärde. Värmeutveckling under malning kan vara skadlig för vissa livsmedel (t.ex. aromatiska kryddor och kaffebönor kan förlora arom om de överhettas). Därför är malningsutrustning med god kylning eller kort uppehållstid att föredra.
För många pulver inom livsmedel (barnmat, pulversåser, kakaopulver, proteinpulver m.m.) är partikelstorleksfördelningen viktig för exempelvis upplösning i vatten eller mun-känsla.
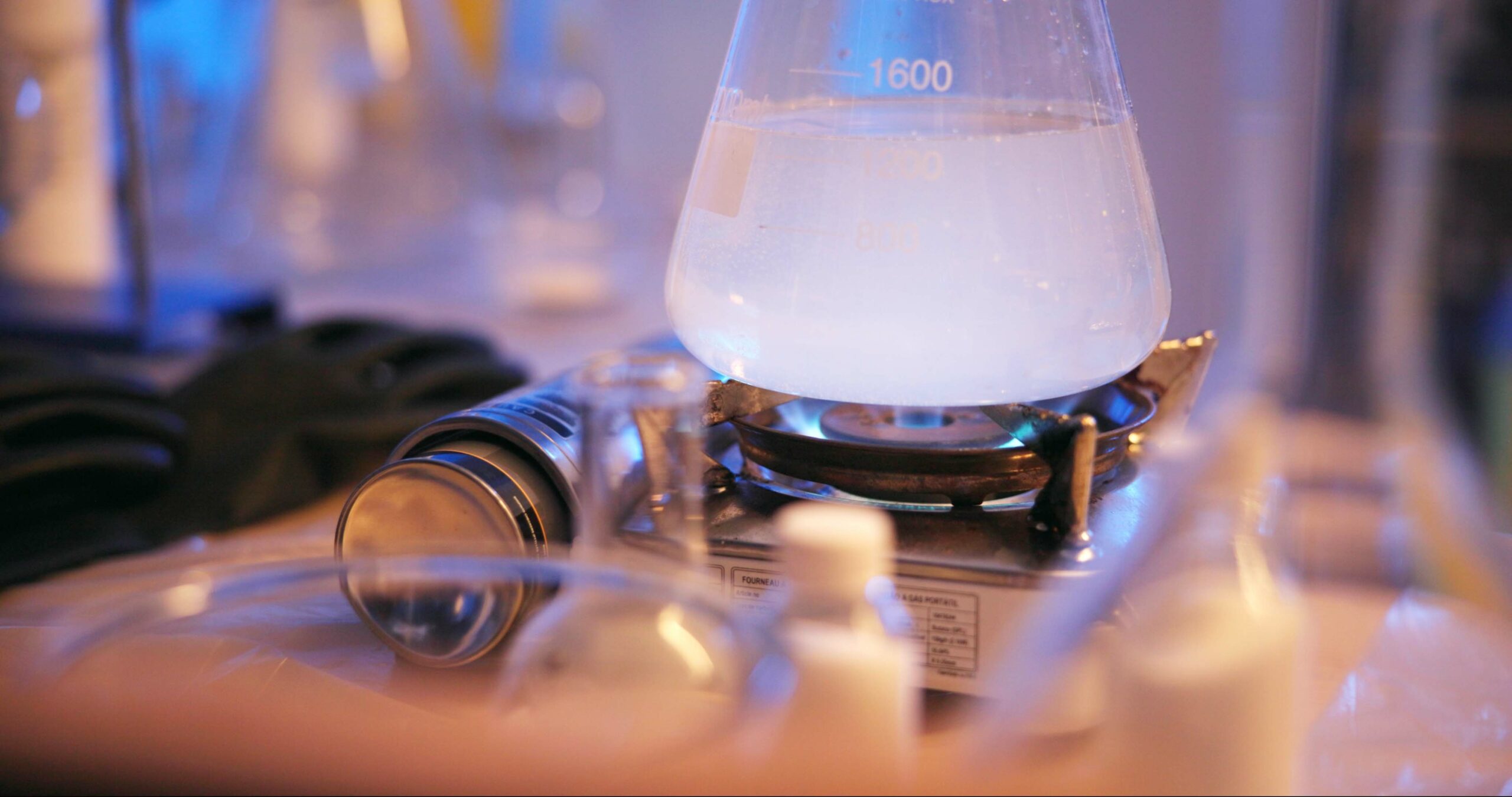
Kemisk industri
Inom den kemiska industrin och närliggande sektorer (såsom färg- och lackindustrin, plast- och gummiindustrin samt tillverkning av gödningsmedel) spelar malning en viktig roll för att uppnå rätt materialegenskaper. Exempelvis kräver tillverkning av färgpigment att fasta pigmentpartiklar mals ned till mikrometerstorlek för att färgen ska bli homogen och ha rätt täckförmåga. Kulkvarnar, pärlkvarnar eller liknande används ofta för att finfördela pigment i en vätska eller i färgslurry. Inom polymerkemi kan malning användas för att pulverisera plastgranulat eller gummimaterial till pulverform (t.ex. för återvinning eller för att blanda in additiv). Gödselmedel som urea och fosfater kan malas till fint pulver för att underlätta blandning och spridning. Även katalysatorer och andra fasta kemikalier mals ofta till pulver för att öka den aktiva ytan.
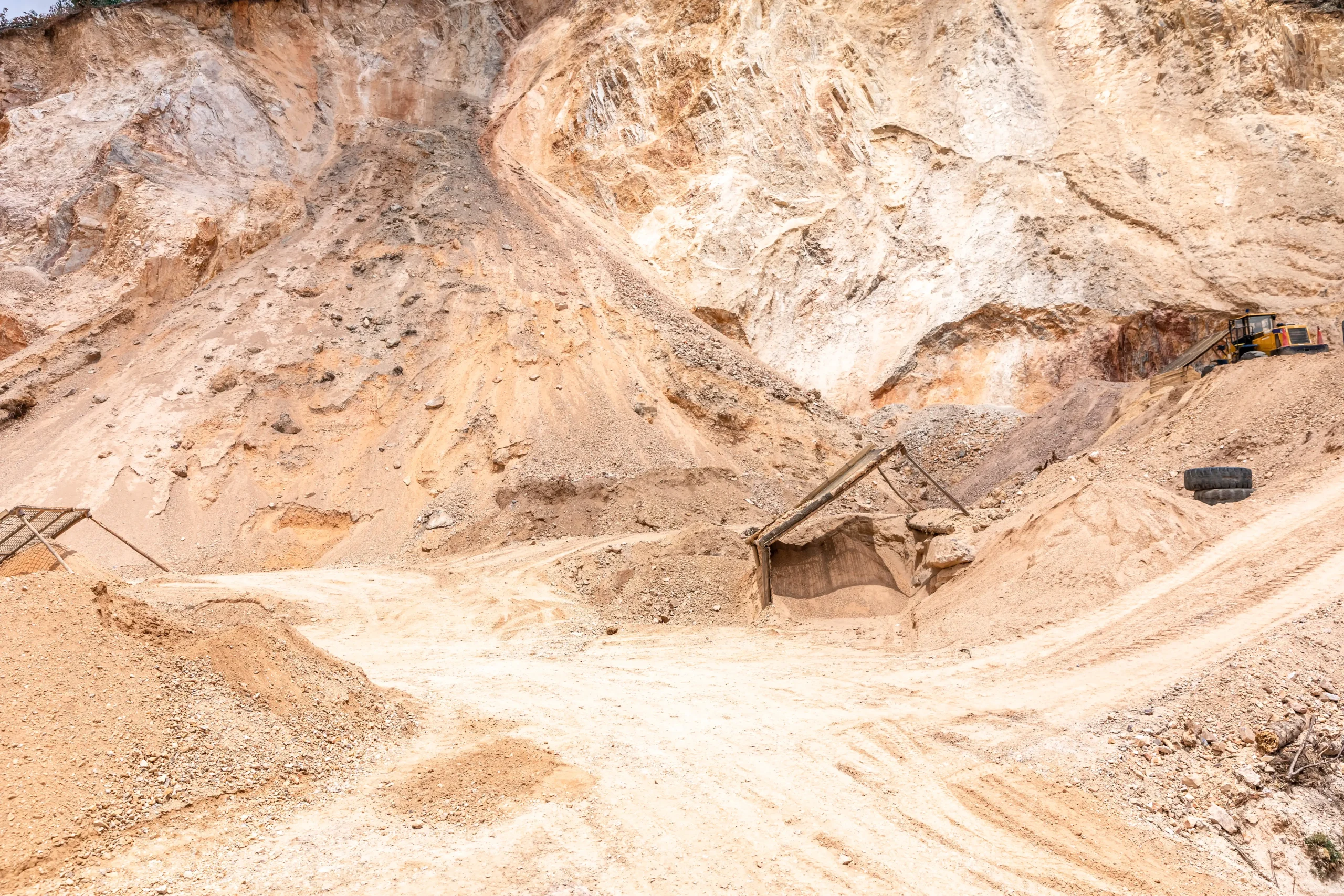
Gruvindustri
Gruvindustrin är en sektor där malning kanske används mest omfattande sett till volym. Här handlar det om att mala tonvis av malm per timme för att extrahera metaller eller mineraler. Efter sprängning och grovkrossning av berg i gruvan transporteras malmen till anrikningsverket där den först krossas och sedan mals i stora roterande trumkvarnar. Typiska maskiner är kulkvarnar och stavkvarnar (som liknar kulkvarnar men använder långa stålstänger som malmedia).
Dessa roterande kvarnar kan vara flera meter i diameter och hantera mycket stora flöden. Malningen fortgår tills malmen blivit som en fin sand eller slurry, så att värdefulla mineral som järnmalm, koppar, guld etc. frigörs från gråberget. Därefter kan de värdefulla partiklarna separeras ut genom anrikning (flotation, magnetism eller annan teknikberoende på mineral.) I gruvsammanhang är energiförbrukningen en stor fråga – malning är en av de mest energikrävande delarna av malmförädlingen. Utrustningen måste vara extremt robust och tåla kontinuerlig drift med slipande material.
Betydelsen av precisionsmalning
I takt med att kraven på produktkvalitet och processeffektivitet ökar har exakt och precisionsstyrd malning blivit allt viktigare. Precisionsmalning handlar om att noggrant kontrollera slutproduktens partikelstorlek och fördelning samt minimera oönskade biprodukter (som för mycket fint damm). Flera skäl gör detta viktigt:
- Produktkvalitet och konsistens: Många produkter – särskilt läkemedel, men även livsmedel och kemikalier – kräver en specifik partikelstorleksfördelning för att fungera optimalt. Om fördelningen kan hållas snäv (d.v.s. de flesta partiklar inom ett begränsat storleksintervall) så blir mer av produkten inom specifikation och mindre behöver kasseras eller omarbetas. För läkemedel är en snäv partikelfördelning avgörande för att säkerställa doseringsenhetlighet och biotillgänglighet i varje batch. Inom färg- och pulverindustrin ger en jämn partikelstorlek enhetliga egenskaper (t.ex. jämn färg, konsistent reaktivitet). Precisionsmalning möjliggör att man träffar rätt partikelstorlek varje gång, vilket ger förutsägbarhet i vidare process och slutprodukt.
- Förbättrat flöde och hantering: Genom att undvika extrema avvikelser i partikelstorlek förbättras pulverflödet. Mycket fines (extremt små partiklar) tenderar att orsaka dammbildning, klumpning och dåligt flöde, medan för stora partiklar kan segreggera eller fastna i matningsutrustning. En kontrollerad malningsprocess ger ett pulver som beter sig konsekvent i silos, matarskruvar och pressar. Till exempel i en tablettmaskin kan inkonsekvent pulverflöde leda till variationer i tablettvikt och inhomogen fördelning av aktiv substans. Genom precisionsmalning minimeras dessa problem – pulvret fyller ut matriserna likformigt och ger tabletter med jämn vikt och innehåll.
- Process- och maskinstabilitet: Om partikelstorleken håller sig inom de avsedda gränserna slits utrustningen jämnare och oväntade driftstopp kan undvikas. Överskott av fina partiklar kan orsaka beläggningar, igensättningar av filter eller ökat slitage på pumpar och transportörer. Dessutom kan för mycket fint damm skapa explosionsfara i vissa miljöer (t.ex. mjöltavsexplosioner i silor). Genom att styra malningen och kanske integrera avskiljning (t.ex. luftklassificering för att ta bort överkorn eller underkorn) ser man till att endast material av önskad storlek går vidare. Detta ger en stabilare process och färre avvikelser. Inom validerade industrier som läkemedel är det också ett krav att processen är reproducerbar – man måste kunna lita på att malningen ger samma resultat från gång till gång, vilket kräver precision.
- Högre utbyte och mindre spill: En okontrollerad malning kan antingen under-mala (ge för grovt material som måste malas om) eller över-mala materialet. Båda fallen innebär ineffektivitet och potentiellt svinn. Övermald produkt blir till onödiga fines som kanske inte kan utnyttjas och ofta måste kasseras eller hanteras separat. Dessa fina dammpartiklar bidrar inte till produktens funktion men utgör spill och kan dessutom medföra mer städning och filterunderhåll i anläggningen. Genom precisionsstyrd malning undviker man att skapa överskott av sådana oanvändbara partiklar – man siktar på ”lagom” finhet. Mindre spill innebär högre totalutbyte av råvaran till färdig produkt och minskade kostnader för avfallshantering. Dessutom minskar behovet av att städa upp damm i produktionsmiljön, vilket sparar både tid och slitaget på utrustningen.
- Undvika kvalitetsfel och omarbete: I exempelvis tablettillverkning kan felaktig partikelstorlek leda till allvarliga kvalitetsbrister. För stora partiklar kan orsaka ojämn blandning, medan för mycket fint pulver kan ge problem vid komprimering – tabletter kan skikta sig eller spricka (”capping” och laminering) om pulvret är för finmalt och luftigt. Precisionsmalning innebär att man optimerar partikelstorleken så att pulvret varken är för grovt eller för fint, utan ”lagom” för att ge starka tabletter utan defekter. Detta minskar behovet av att kassera eller omarbeta batcher som inte uppfyller specifikation. I andra industrier, som beläggningar eller 3D-printingpulver, kan fel partikelstorlek leda till ytdefekter eller dålig processbarhet – också det undviks genom strikt malningskontroll.
Slutsats
Malning utgör ett ofta osynligt men fundamentalt led i processindustrin – från gruvornas gigantiska kvarnar som förbrukar megawatt av energi, till läkemedelsfabrikens prydliga konkvarn i rostfritt stål. Genom att förstå malningsprocessens syfte (att skapa en lämplig partikelstorlek och fördelning) och genom att välja rätt metod och utrustning för rätt applikation, kan ingenjörer och tekniker säkerställa hög produktkvalitet, driftsäkerhet och effektivitet. Precisionsstyrd malning har blivit nyckeln till att uppfylla moderna kvalitetskrav: en snäv partikelstorleksfördelning förbättrar blandningars homogenitet, tabletters funktion och pulverflöden, samtidigt som spill och omarbete minskar.
Den tekniska utvecklingen inom malningsutrustning – såsom Hanningfields Uni-Mill konkvarnar – ger idag möjlighet att skala upp processer från labb till fullskalig produktion med bibehållen kontroll. Detta innebär att processindustrins aktörer, vare sig det är läkemedelsföretag, livsmedelsproducenter eller kemikalietillverkare, har verktygen att optimera sina malningssteg för framtiden. Med rätt kvarn på rätt plats kan man mala med precision – och därigenom skapa produkter som möter både industrins och samhällets högt ställda krav på kvalitet och prestanda.
Synonymer:
Synonymer till malning beroende på sammanhang:
Vid bearbetning av material (t.ex. spannmål, mineraler, metall):
- krossning
- pulverisering
- finfördelning
- slipning (vid hårdare material)
- rivning (vid vissa typer av livsmedel)
I industriell eller teknisk kontext:
- fragmentering
- nedmalning
- granulering (om målet är att uppnå kornig struktur)
- mikronisering (vid mycket fin malning, till mikronnivå)
Inom livsmedelsberedning (t.ex. kaffe, kött):
- malning
- köttkvarnning (vid kött)
- malprocess
- bryggberedning (när det avser malningsgraden för kaffe)
Vid överförd eller mer allmän betydelse (t.ex. tråkigt, monotont arbete):
- nötning (även bildligt)
- slit
- rutinarbete
Vanliga frågor och svar (FAQ)
Vilka effekter kan korrekt respektive felaktig malning ha på produkten?
Korrekt utförd malning har positiva effekter på produkten. När partikelstorleken hålls inom rätt intervall och fördelningen är jämn får man en högre och jämnare produktkvalitet. Till exempel säkerställer enhetlig malning att varje tablett i en läkemedelsbatch väger ungefär lika mycket och innehåller samma mängd aktiv substans. En jämn partikelstorlek förbättrar också pulverflödet vid hantering och dosering, samt kan ge bättre löslighet för ämnen som ska lösas upp (viktigt för t.ex. läkemedel och livsmedel). Dessutom kan en skonsam malningsprocess bevara materialets egenskaper – en bra kvarn genererar minimalt med värme och förstör inte känsliga komponenter i produkten. Många moderna malningsmaskiner är utformade för att inte kontaminera produkten; exempelvis har högkvalitativa kvarnar ingen metall-mot-metall-kontakt invändigt, vilket förhindrar att metallfragment slits av och hamnar i pulvret.
Felaktig eller bristfällig malning kan däremot försämra produktens egenskaper. Om malningen ger ojämn partikelstorlek kan det leda till inhomogen produkt – i läkemedel kan detta innebära variationer i dos per enhet, och i livsmedel kan vissa partier av produkten bli grövre eller finare än avsett. Ojämnheter kan orsaka segregationsproblem (att finare partiklar separeras från grövre under transport eller blandning) vilket resulterar i inkonsekvent kvalitet. Ett konkret exempel är att ojämn malning kan ge tabletter med varierande vikt och halt av aktiv substans, eller att en kryddblandning smakar olika starkt i olika skedar på grund av dålig partikeluniformitet.
Överdrivet finmalet pulver kan också skapa problem: mycket fint damm är svårhanterligt, kan klumpa sig eller orsaka statiska problem, samt innebära spill och svinn. I industrin noterar man att pulverformuleringar kan skapa betydande damm och spill vid malning och hantering, vilket minskar utbytet och kräver extra åtgärder för att tas om hand. Ur arbetsmiljösynpunkt kan för mycket luftburet damm även vara en hälso- och explosionsrisk i extrema fall (t.ex. vid malning av organiska material som mjöl eller trä). Slutligen kan fel inställd malningsutrustning (eller en olämplig kvarntyp) alstra onödig värme eller kraft som degraderar materialet – värmekänsliga ämnen kan tappa effekt eller ändra egenskaper om de mals för hårt eller för länge.
Vilka typer av maskiner används för malning, och vad är en konkvarn (konisk kvarn)?
Det finns en mängd olika kvarntyper och malningsutrustningar, anpassade efter materialets egenskaper och önskat resultat. Några vanliga kategorier av malningsmaskiner är:
- Hammarkvarnar: Utrustade med roterande hammare eller slagpinnar som krossar materialet mot en fast yta eller genom en skärm. De används ofta för grov till medelfin malning av t.ex. spannmål, träflis eller återvinningsmaterial. Hammarkvarnar är robusta och kan hantera stora volymer, men de tenderar att ge upphov till mer fint damm och värme jämfört med vissa andra kvarntyper.
- Kulkvarnar: Cylinderformade kvarnar som roterar med malmedier inuti (ofta stålkulor eller keramiska kulor). När cylindern snurrar slår och gnider kulorna mot materialet så att det mals. Kulkvarnar används både i laboratorium och industri (t.ex. inom gruvindustrin för malm) och kan ge mycket finmalet resultat. De är mångsidiga – kan användas för våt- eller torrmalning – men malningsprocessen kan vara relativt långsam och energikrävande.
- Jetkvarnar (luftstrålekvarnar): En teknik där materialet finfördelas genom att partiklarna kolliderar med varandra i en ström av högtrycksluft eller gas. Jet mills saknar rörliga delar som krossar; istället accelereras pulverpartiklar i en gasström och pulveriseras vid kollision. Detta möjliggör extra fin malning (ner mot mikron-storlek) med minimal värmeutveckling, vilket är värdefullt för extremt värmekänsliga eller rena applikationer (t.ex. vissa läkemedel och specialkemikalier). Jetkvarnar ger mycket fin produkt men lämpar sig bäst för mindre batcher eller högt värde-material, då energiförbrukningen är hög.
- Koniska kvarnar (Konkvarnar): Detta är en typ av kvarn med en roterande impeller (rotor) inuti en konformad sikt (sil). Materialet matas in och impellern pressar det genom öppningarna i den perforerade kon-sikten, vilket gradvis mals ner till den partikelstorlek som motsvarar hålens storlek. En konkvarn, till exempel Hanningfields Uni-Mill, är utformad för att ge enhetlig och kontrollerad partikelstorlek med hög effektivitet. Den koniska designen ger en skonsam men effektiv malning där partiklarna snabbt bryts ner utan att övermala materialet. Detta resulterar i ett jämnt pulver med minimal andel väldigt fina partiklar (mindre ”damm”) och låg värmeutveckling. Tack vare den mildare behandlingen påverkas inte känsliga ämnens kemiska stabilitet, och maskinen undviker metallisk kontaminering genom att inga ytor gnids metall-mot-metall. Konkvarnar är vanliga inom läkemedel, livsmedel och kemisk industri, där man ställer höga krav på konsekvent partikelstorleksfördelning och hygien. Hanningfield Uni-Mill är ett exempel på en sådan kvarn som kombinerar hög kapacitet med enkel rengöring och repeterbara resultat. Den kan användas för både torr- och våtmalning och finns i olika storlekar, vilket gör den flexibel för olika produktionsbehov.
Hur påverkar matningshastigheten resultatet vid malning?
Matningshastigheten – det vill säga hur snabbt material förs in i kvarnen – påverkar hur länge materialet stannar i malningszonen och därmed hur mycket det finfördelas. Vid för låg matningshastighet stannar materialet längre i kvarnen, vilket kan resultera i övermalning. Det kan leda till att alltför små partiklar bildas (s.k. ”fines”), vilket försämrar flödesegenskaper och kan medföra spill eller dammbildning. Omvänt kan för hög matningshastighet leda till att materialet inte hinner malas tillräckligt innan det passerar genom sikten, vilket ger ett grovt och ojämnt resultat.
Inom processindustri används därför ofta kontrollerad matning, till exempel genom vibrationsmatare, rotationsventiler eller vacuumöverföring, för att säkerställa jämnt materialflöde och optimalt tryck mot sikten. I vissa system används även vågar för att dosera rätt mängd material per tidsenhet. En stabil och reproducerbar matning är särskilt viktig i skalbara processer, eftersom variationer i matningshastighet gör det svårt att jämföra batcher eller överföra metoden till större skala.
Kan man mala både våta och torra material i samma maskin?
Vissa kvarntyper, särskilt koniska kvarnar som Hanningfield Uni-Mill, är konstruerade för att kunna hantera både torrmalning och våtmalning i samma maskin, beroende på konfiguration. Torrmalning är vanligast – pulver, granulat och torra agglomerat matas in och mals ned mekaniskt. Våtmalning används när materialet är fuktigt, efter granulering, eller när partiklarna annars skulle damma, vara svårhanterliga eller skapa explosiv atmosfär.
För att hantera våtmalning krävs att kvarnen har tillräcklig tätning, rätt ytskikt och ofta någon form av rengöringsfunktion, exempelvis WIP (Wet-In-Place) eller CIP (Clean-In-Place). Uni-Mill kan utrustas med dessa system och har även möjligheter för inbyggd temperaturkontroll, vilket kan vara viktigt vid våtmalning där värmeutveckling riskerar att påverka produktens egenskaper. Samma kvarn kan därmed användas för båda typerna av malning, men det kräver korrekt konfiguration och ibland byte av verktyg (t.ex. impeller eller sikt).
Vad menas med skalbarhet i malningssammanhang och varför är det viktigt?
Skalbarhet innebär att resultatet från en malningsprocess i liten skala – exempelvis i laboratoriet – går att upprepa i större skala vid pilot- eller fullskalig produktion. Detta är särskilt viktigt inom läkemedel, livsmedel och kemi, där man först testar och optimerar processer i liten volym.
För att en process ska vara skalbar krävs att samma principer och parametrar kan appliceras på större mängd material utan att resultatet förändras. Exempelvis måste partikelstorleksfördelning, värmeutveckling och flödesegenskaper vara jämförbara oavsett volym. Här är koniska kvarnar fördelaktiga, eftersom samma kvarntyp finns i flera storlekar och har utbytbara delar (sikt, impeller) med liknande geometri. Det gör att man kan gå från 1 kg till 1000 kg utan att behöva byta teknik.
Om en kvarn saknar skalbarhet riskerar man att få avvikande resultat i större batcher – vilket kan leda till omarbete, avfall eller att produkten inte godkänns enligt kvalitetskraven. Skalbar malning är därför en förutsättning för repeterbar och kostnadseffektiv produktion.